Lithium-Ion Battery Recycling and Reuse
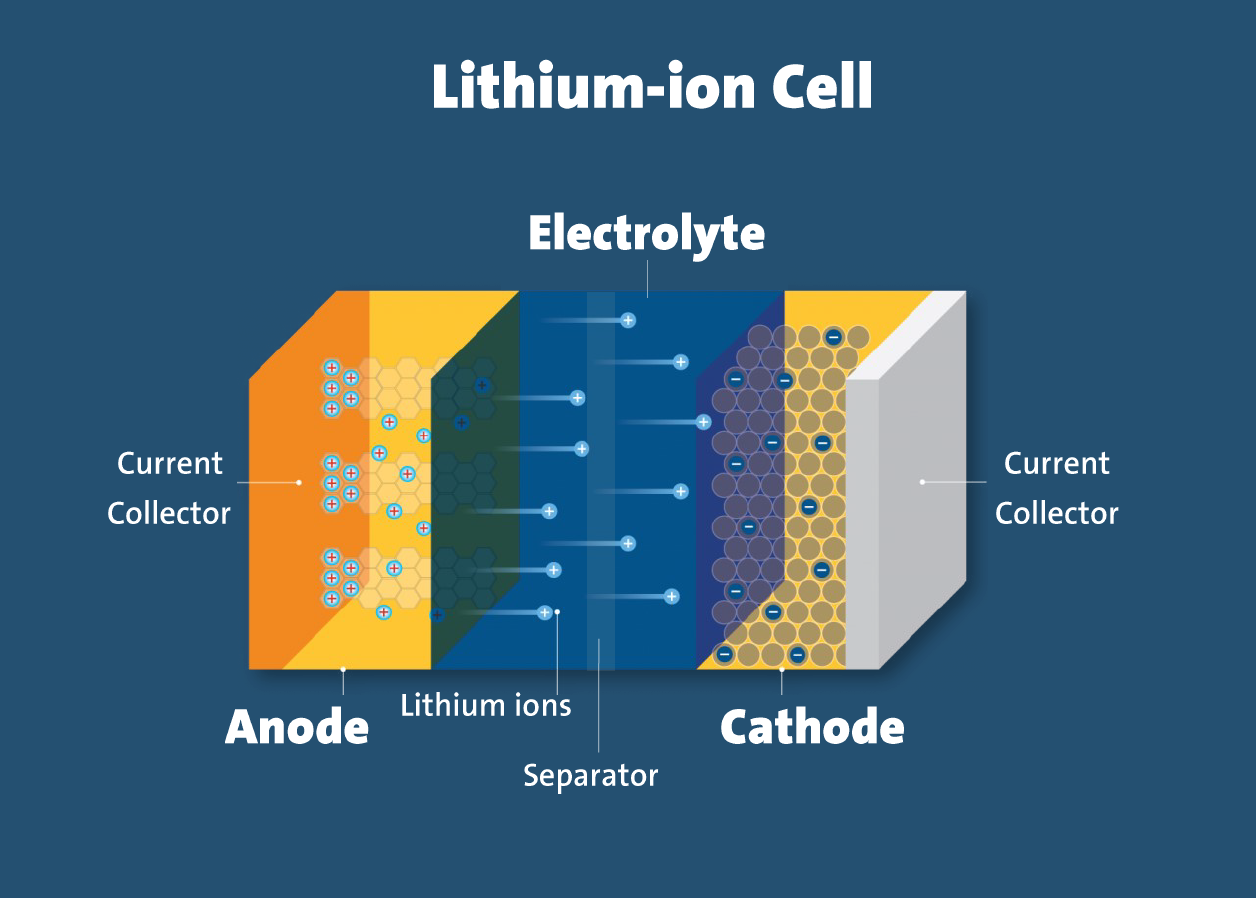
Lithium-Ion Battery Recycling and Reuse
Safe recycling of lithium-ion batteries at the end of their lives conserves the critical minerals and other valuable materials that are used in batteries and is a more sustainable approach than disposal. Although there is not one path that all batteries take at the end of their lives, lithium-ion battery recycling usually follows a similar series of steps.
In the typical first step, consumer electronics, batteries, and battery-containing devices are collected by the retailer who sold the replacement item, by a storefront e-waste collector, or by a business that specializes in collecting other companies’ used electronics. Electric vehicle batteries may end up at a dealership or automobile mechanic shop, if the vehicle’s battery needs to be replaced, or at an automobile disassembler if the entire vehicle reached the end of its life. In all cases, batteries then need to be identified and sorted for proper recycling and may change hands several times in the process, getting shipped to other collection facilities before arriving at a facility that can process them. Larger battery packs, such as those from electric vehicles, could be partially disassembled at any time in this process into cells or modules to make transportation, storage, and processing easier.
Some battery packs or modules may also be evaluated for repair or reuse—either being put back into a device similar to their original one or being repurposed in a different type of product or application. For example, some companies are experimenting with repurposing used electric vehicle batteries to store excess electricity generated by solar panels. Battery packs that can be repaired may have one or more “bad” modules replaced before being put back into use in the original or other appropriate applications.
When a battery is sent for recycling after collection and evaluation, a common next management step is shredding. Depending on the size of the shredding equipment, part or all of the battery is shredded. In some cases, a portion of a device containing a battery may also be shredded. The batteries are either discharged to remove electricity before this step or are otherwise managed to prevent fires during shredding. Many battery recyclers are also accepting battery materials in the form of manufacturing scrap for processing.
The shredding operation creates a number of different streams, including the following:
- “Black mass”” (a granular material made up of the shredded cathodes and anodes of the batteries).
- Copper and aluminum foils (which held the anode and cathode material).
- Separators (thin plastic films).
- Other plastics.
- Steel canisters.
- Electrolyte.

Black mass contains the materials that can be further processed and made into new battery cathodes and anodes. Although the term “black mass” is commonly used, there are no industry standards for black mass. Depending on the batteries shredded and the type of shredding, there can be wide variation in the exact make-up and amount of liquid in this material. Black mass is frequently then sent to another facility that recovers the valuable metals (like cobalt, nickel, and sometimes lithium). Black mass may also be exported for this purpose. Other output materials, such as foils and steel canisters, may also be recycled through separate, dedicated pathways.
Although innovations are happening quickly in lithium-ion battery recycling, currently there are two main methods to recover the metals out of black mass:
- A heat-based smelting process (pyrometallurgy).
- A liquid-based leaching process (hydrometallurgy).
In some cases, the heat-based process can also be used to recover metals from batteries without an initial shredding step. Generally, smelting can recover cobalt and nickel, but it would take additional steps to recover other critical materials like lithium from the residue left behind. Recycling technologies that use leaching may be able to economically recover high amounts of cobalt, nickel, lithium, and manganese and several facilities are in development in the United States.
After smelting or leaching, the recovered metals must be processed further to be made into new batteries. At this point, the processing would look similar or identical to making battery components out of non-recycled metals.
In addition to the two main recycling techniques, some researchers and recyclers are experimenting at smaller scale with a technique called direct recycling in an effort to bring it to market. Direct recycling, sometimes called “cathode to cathode recycling,” saves energy by preserving the highly engineered cathode structure that is the most valuable part of the lithium-ion battery and reducing the amount of manufacturing needed to recycle these materials into a new battery.
Lithium-Ion Battery Recycling and Reuse
Reuse and repurposing are two similar, environmentally friendly alternatives to recycling or disposal of a lithium-ion battery that no longer meets its user’s needs or is otherwise being discarded. Battery performance degrades over time, but used batteries can still provide useful energy storage for other applications. For example, an electric vehicle battery that no longer holds enough energy to cover the range its owner desires could be reused as an electric vehicle battery for someone who requires less range from their vehicle, or it could be repurposed into a battery for storing energy from solar panels.
Reuse and repurposing options are still being developed, but could someday provide batteries a “second life” on a larger scale before they get recycled. This second life would benefit the environment by extending the useful life of the battery and decreasing resource demands for making new batteries.
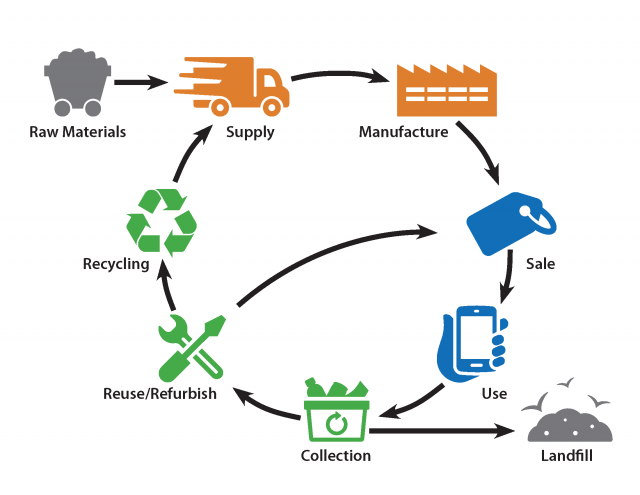